Thermal assembly, a cornerstone of modern manufacturing, encompasses a spectrum of techniques and specialized equipment tailored to meet diverse bonding needs. From the intricate components of automobiles, boasting over 30,000 parts, to the delicate specifications of medical devices subject to stringent FDA guidelines, the efficacy of thermal assembly can make or break the integrity of the final product.
Mastering Thermal Assembly Processes and Techniques
At the heart of thermal assembly lie sophisticated systems like our renowned C-Series and H-Series Thermal Press systems. These cutting-edge tools leverage heat sealing and heat staking techniques to forge robust bonds in heat-sensitive materials, ranging from films and foils to various plastics.
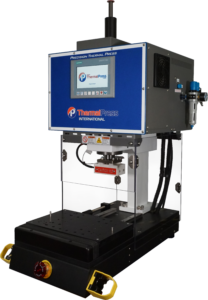
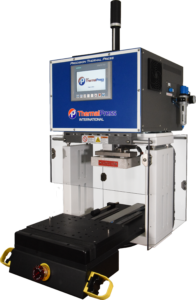
Thermal Heat Staking: Precision in Plastic Bonding
Heat staking, also known as thermoplastic staking, emerges as the go-to method for melding plastic materials like ABS and polypropylene. It typically involves the process of joining two dissimilar plastic materials or joining metal and plastic parts together. Heat and pressure are used to soften a specific area of the thermoplastic component enough to allow it to reform. This specific area is then molded into a new shape or profile that forms over and/or around the connecting part. Once cooled, the reformed plastic will hold the mated part in place. This method stands tall, particularly in realms such as sensitive electronics found in medical devices, where traditional ultrasonic heat-sealing methods may introduce unwanted vibrations and mechanical stress, imperiling the integrity of critical components like medical monitors and insulin pumps.
Thermal Heat Sealing: Forging Unyielding Bonds
Heat sealing, or heat welding, represents a pinnacle in joining thermosensitive plastics like PVC and vinyl. By subjecting materials to elevated temperatures, they undergo controlled softening, fostering a seamless fusion. This versatile technique, which can be executed through hot bar, impulsive heat, induction, and ultrasonic means, finds applications ranging from mundane, like sealing potato chip bags, to pivotal, such as ensuring the integrity of heat seal connectors (HSCs) and medical components facing rigorous pressure and vacuum conditions.
Tailored Solutions for Every Need
The efficacy of thermal assembly hinges not only on technique but also on the right machinery. Our diverse lineup caters to an array of requirements, ensuring optimal performance across various applications:
- C-Series: Versatile and adaptable, our flagship machine accommodates a wide spectrum of part sizes and shapes, embodying the pinnacle of thermal assembly technology.
- H-Series: Engineered for formidable force, the H-Series boasts an H-Frame design tailored for high-pressure applications, all while remaining low profile enough to fit seamlessly onto standard workbenches.
- MicroLAB: Designed with more compact components in mind, the MicroLAB inherits all the capabilities of its larger counterparts, offering uncompromising performance in a smaller footprint.
- Manual Thermal Press: Ideal for smaller-scale production runs and rapid prototyping, our manual press delivers precision and flexibility in a streamlined package.
- Multi-WorkStation System: Built for scalability and efficiency, this modular solution enables simultaneous process of multiple parts of assemblies. Ideal for high-throughput environments, it integrates seamlessly with automation and supports complex workflows without sacrificing precision.
Embrace Reliability with Thermal Press International
Since our inception in 1976, Thermal Press International has stood at the vanguard of thermal assembly machinery. Crafted with precision in our state-of-the-art facility in Livermore, California, our compliant, top-grade machinery embodies the epitome of American engineering prowess, ensuring that your assembly needs are met with unmatched reliability and efficiency. Whether you’re navigating the intricate landscape of automotive assembly or pioneering breakthroughs in medical technology, our thermal assembly solutions stand as your steadfast ally in the pursuit of excellence.
Contact Us: Contact Thermal Press International at (925) 454-9800 to speak with an engineer and explore how heat staking can optimize your manufacturing operations.