In the world of thermoplastic assembly, precision and strength are paramount. Among the various techniques used to join plastic components, heat staking and heat swaging stand out for their efficiency and reliability. While these terms are often used interchangeably, it’s essential to understand that heat swaging is a specialized form of heat staking. In the blog post, we’ll explore what heat swaging is, how it fits under the umbrella of heat staking, and its common application in thermoplastic assembly.
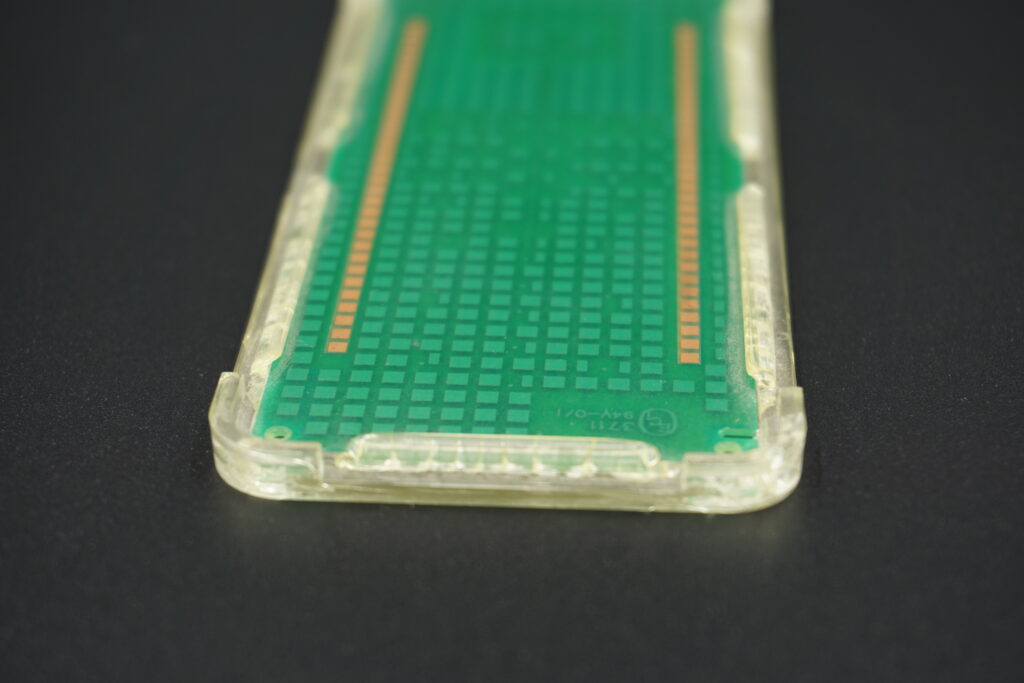
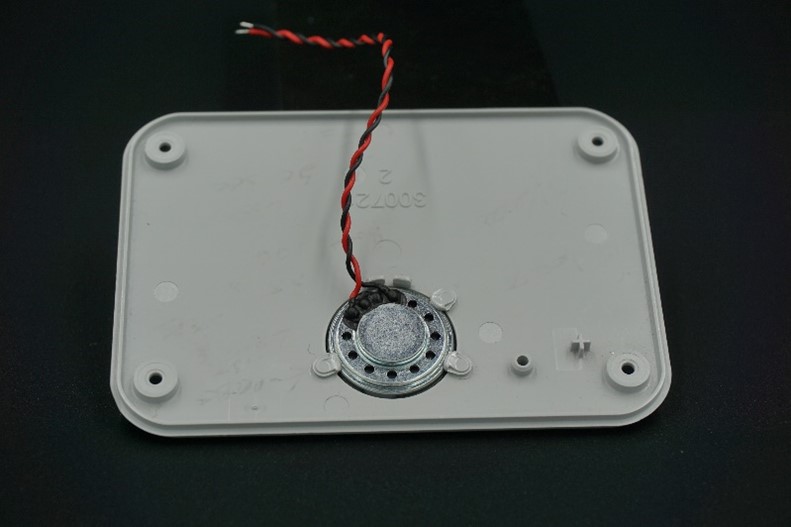
Understanding Heat Staking
Heat staking is a process where a heated tool is used to melt and reshape plastic stakes or posts that protrude through another part. This reshaping forms heads or rivets, creating a strong mechanical bond that holds the parts together. Heat staking is widely used in various industries, including automotive, electronics, medical devices, and consumer products, due to its ability to produce durable, reliable joints without additional fasteners or adhesives.
What is Heat Swaging?
Heat swaging, on the other hand, is a specific application of heat staking. It involves using a heated tool to deform and reshape plastic components, such as collars, ridges, or flanges, to create a mechanical interlock with another part. While the fundamental principle of applying heat and pressure remains the same, heat swaging focuses on reshaping features other than stakes or posts to secure parts together.
Common Applications of Heat Swaging
Heat swaging is particularly useful in applications where reshaping specific features of the plastic part is necessary to achieve the desired bond. Here are some common uses of heat swaging in thermoplastic assembly:
Automotive Industry
Interior Components: Heat swaging secures plastic trim pieces, dashboards, and other interior components by reshaping flanges or ridges to create a robust mechanical interlock.
Under-the-Hood Applications: It is used to attach plastic covers, shields, and components in the engine compartment, providing durable connections that withstand high temperatures and vibrations.
Consumer Electronics
Device Enclosures: Heat swaging assembles plastic housings and secures internal components in devices like smartphones, tablets, and wearable electronics, ensuring a tight, reliable fit.
Connectors: It forms and secures plastic parts in electrical connectors and ports, providing strong, durable joints that withstand repeated use.
Medical Devices
Device Housings: Heat swaging ensures secure and sterile enclosures for medical devices by reshaping plastic features to lock parts together.
Diagnostic Equipment: It is used to attach plastic components in diagnostic sensors and equipment, maintaining precision and reliability.
Household Appliances
Small Appliances: Heat swaging assembles plastic parts in blenders, coffee makers, vacuum cleaners, and other household appliances, providing robust and reliable connections.
Large Appliances: It secures plastic components in washing machines, refrigerators, and dishwashers, enhancing their durability and performance.
The Heat Swaging Process
The heat swaging process involves several key steps to ensure strong, reliable bonds between plastic components:
- Preparation: Parts are designed with features like collars, ridges, or flanges that can be reshaped during the swaging process. Custom fixtures are used to hold the parts in place and ensure accurate alignment.
- Heating: A tool, typically made of metal, is heated to a specific temperature suitable for the type of plastic being used. Precise temperature control is crucial to soften the plastic without burning or degrading it.
- Swaging: The heated tool is pressed against the plastic part, applying heat and pressure. The plastic softens and deforms under pressure, creating a mechanical interlock with the other part.
- Cooling: The deformed plastic cools and solidifies, retaining its new shape and forming a strong, durable bond. The tool is then removed, and the assembled parts are taken out of the fixture.
Conclusion
Heat swaging, as a specialized form of heat staking, plays a vital role in thermoplastic assembly. Its ability to create strong, precise, and reliable bonds without additional materials makes it an ideal choice for various industries, from automotive and electronics to medical devices and household appliances. By understanding the nuances of heat swaging, manufacturers can leverage this technique to enhance the durability and performance of their plastic assemblies.