Introduction:
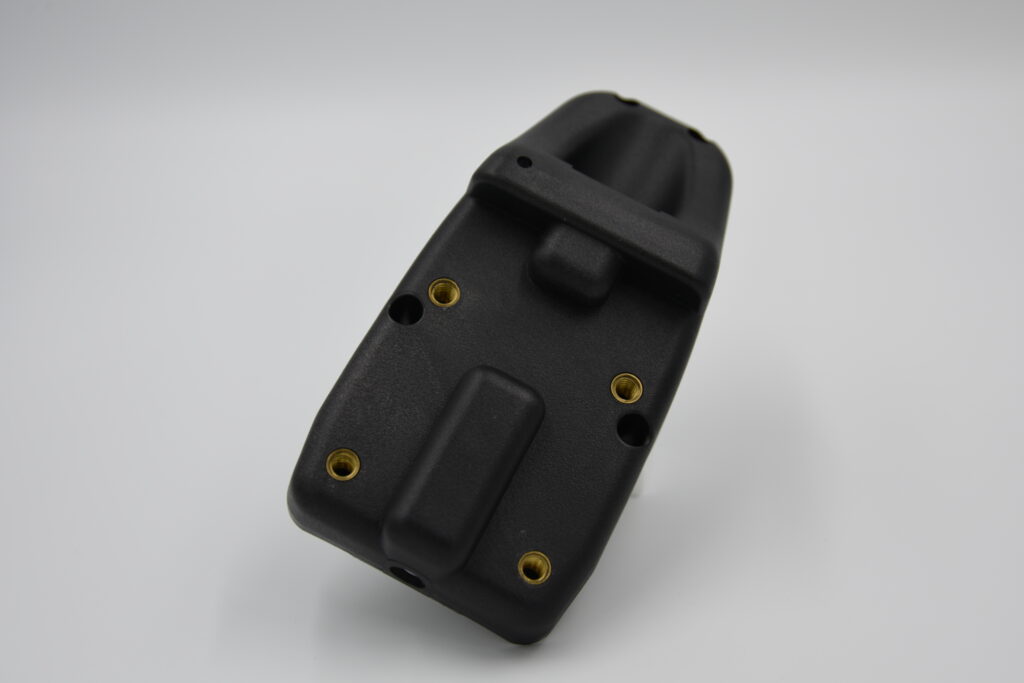
In the realm of product design, the choice of materials often plays a critical role in determining the functionality and longevity of a product. Plastic, with its versatility and affordability, is a popular choice for various components, including housings for electronic devices, automotive parts, and consumer goods. However, when it comes to assembling plastic housings, ensuring the integrity of threaded connections can be a challenge. This is where thermal insertion of threaded inserts emerges as a game-changer, offering a robust solution for securely fastening components to plastic housings.
Understanding Thermal Insertion:
Thermal insertion is a process used to install threaded inserts into plastic components by heating the insert and pressing it into the designated hole. The principle behind thermal insertion is simple yet effective: heat softens the plastic, allowing the insert to be easily embedded, and upon colling, the plastic solidifies, creating a strong, permanent bond.
Benefits of Thermal Insertion:
Enhanced Strength: By effectively melting into the plastic material, thermal insertion creates a strong mechanical bond between the insert and the housing, ensuring reliable thread engagement and resistance to pull-out forces.
Increased Versatility:
Thermal insertion supports a wide range of plastic materials, including ABS, polycarbonate, nylon, and more, making it suitable for diverse applications across industries.
Time and Cost Efficiency:
Compared to alternative methods such as ultrasonic or press-in insertion, thermal insertion is often faster and requires minimal setup, leading to reduced production costs and shorter lead times.
Consistency and Precision:
Thermal insertion enables precise control over the insertion process, ensuring uniformity across production batches and minimizing the risk of defects or misalignments.
Best Practices for Thermal Insertion:
Proper Design Considerations: Integrating threaded inserts into the initial design phase allows for optimized placement and ensures compatibility with the thermal insertion process.
Material Compatibility:
Selecting inserts and plastic materials with compatible melting points is crucial for achieving strong bond strength and preventing damage to the components.
Temperature and Time Control:
Fine-tuning the heating parameters, including temperature and duration, is essential to prevent overheating or underheating, which can compromise the integrity of the bond.
Quality Assurance:
Implementing stringent quality control measures, such as post-insertion inspection and testing, helps identify any defects or inconsistencies early in the production process.
Applications Across Industries:
From electronic enclosures and automotive assemblies to medical devices and consumer products, thermal insertion of threaded inserts finds widespread application in various industries where reliable fastening of plastic components is paramount. Whether it’s ensuring the structural integrity of a dashboard panel in a car or securing components within a medical device housing, thermal insertion offers a versatile and durable solution.
Conclusion:
In the ever-evolving landscape of manufacturing, the demand for lightweight, durable, and cost-effective solutions continues to drive innovation. Thermal insertion of threaded inserts represents a prime example of how technology can address the challenges associated with assembling plastic components, offering enhanced strength, versatility, and efficiency. By leveraging the principles of heat and pressure, manufacturers can elevate the quality and performance of plastic housing across a myriad of applications, paving the way for more resilient and functional products in the marketplace.