Heat staking is a widely used technique for joining plastic components to non-plastic parts, such as metal or electronic elements, by softening and reforming a plastic post with heat and pressure. The shape of the heat stake post plays a critical role in the strength, durability, and precision of the bond. One of the more specialized and advantageous designs is the rosette-shaped heat stake post. This post design is favored in certain applications for its unique benefits, making it a preferred option in various industries, especially in high-precision assemblies such as electronics, automotive, and medical devices.
What is a Rosette-Shaped Post?
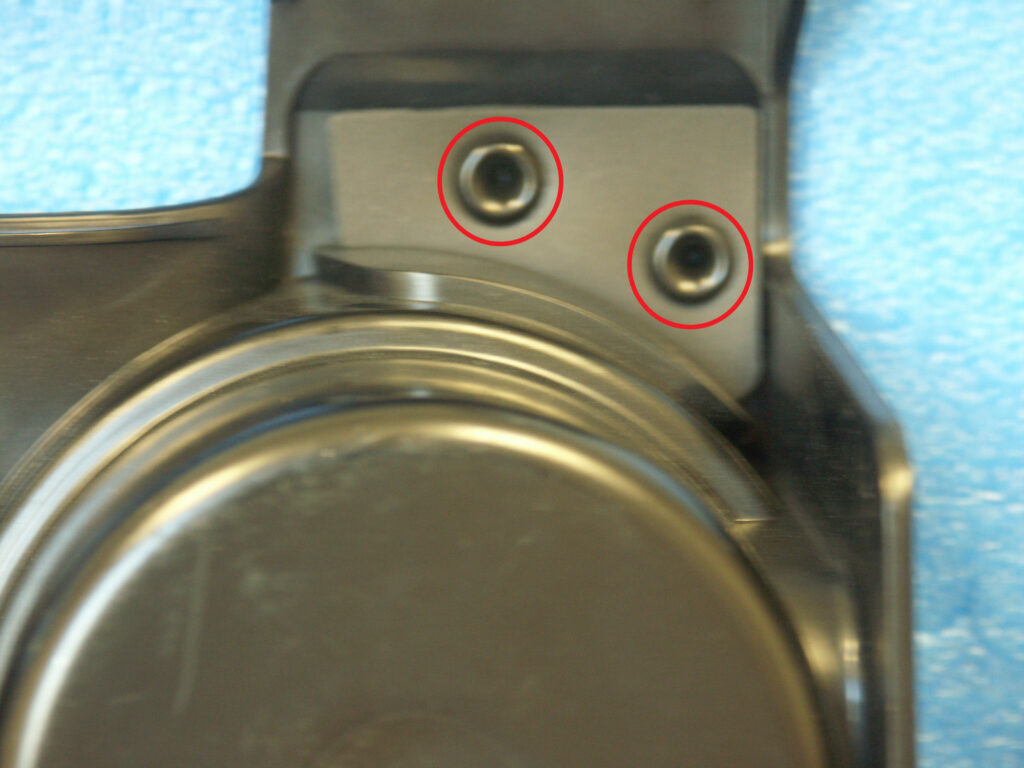
A rosette-shaped heat stake post features a circular or star-like profile with petal-shaped edges. Unlike traditional cylindrical or domed heat stake posts, which simply flatten out during the staking process, the rosette shape allows for more controlled material flow and larger surface area for bonding. The result is a more secure and evenly distributed bond, which provides enhanced mechanical strength and reliability.
Benefits of Rosette-Shaped Heat Stake Posts
- Increased Bond Strength: One of the key advantages of the rosette-shaped post is the improved mechanical interlocking it offers. The petal-like edges of the rosette provide more contact surface area during the staking process, creating a more extensive bond with the surrounding material. This leads to a stronger and more robust joint, which is particularly beneficial in applications where high strength is required to resist mechanical stress or vibration.
- Controlled Material Flow: The unique design of the rosette shape ensures that the plastic material flows outward in a controlled manner during the staking process. This controlled flow reduces the risk of excessive material deformation, ensuring that the stake forms evenly and consistently. This is especially important in delicate assemblies, such as electronics, where precision and consistency are crucial for maintaining the integrity of the surrounding components.
- Even Distribution of Force: Because the rosette shape allows for more even distribution of force across the joint, the resulting bond is less prone to stress concentrations. This reduces the risk of cracking or weakening over time, making rosette-shaped posts ideal for applications where long-term durability is critical.
- Minimized Flashing and Aesthetic Benefits: Heat staking processes often result in flashing (excess material around the stake) due to uncontrolled material flow. With a rosette-shaped post, the controlled flow and even distribution of material minimize flashing, resulting in a cleaner, more aesthetically pleasing finish. This is particularly important in consumer products and visible assemblies where appearance matters.
- Resistance to Torsional Loads: In applications where the joint is subjected to twisting or torsional forces, the rosette-shaped post offers superior resistance compared to standard posts. The shape of the rosette helps lock the plastic into place more securely, reducing the risk of rotation or loosening over time.
- Enhanced Joint Integrity with Thin-Wall Applications: In assemblies with thin walls or lightweight components, traditional cylindrical heat stakes may apply too much force and risk damaging the surrounding material. The rosette-shaped post distributes pressure more evenly, reducing the likelihood of warping or cracking thin parts while still providing a strong, reliable bond.
When and Why a Rosette-Shaped Heat Stake Post is Preferred
Given its distinct advantages, a rosette-shaped post is the preferred option in specific scenarios where mechanical strength, precision, and aesthetics are priorities. Here are some common applications and reasons why manufacturers might choose this post design:
- High-Stress Environments (Automotive and Aerospace): In industries like automotive and aerospace, where components are subject to high mechanical loads, vibrations, and temperature fluctuations, the increased bond strength and resistance to torsional forces offered by rosette-shaped posts make them ideal. Components such as dashboard assemblies, electronic housing, and sensor enclosures benefit from the secure, durable joints that rosette-shaped posts provide.
- Precision Electronics: In electronics manufacturing, where delicate components are housed in plastic enclosures, rosette-shaped posts are often used to ensure precise alignment and secure bonding without damaging sensitive parts. The controlled material flow helps prevent damage to nearby components, ensuring the integrity of the assembly in small, intricate devices like smartphones, wearables, and medical devices.
- Aesthetic Considerations (Consumer Goods): In products where appearance is important, such as consumer electronics or household appliances, manufacturers may prefer rosette-shaped heat stakes due to their clean, minimal flashing and smooth finish. These stakes result in a professional-looking product with less post-processing required to remove excess material or polish the joints.
- Applications Requiring Torsional Resistance: In scenarios where parts may experience rotational forces or torque, such as motor housings or joints in robotics, the rosette-shaped post’s ability to resist torsional loads makes it the preferred choice. The design reduces the risk of loosening over time, ensuring that the joint remains secure throughout the product’s life cycle.
- Thin-Wall Applications: When working with thin or delicate plastic parts, using standard heat staking posts may risk over-pressurizing the material, leading to deformation or cracking. The rosette shape’s ability to distribute force evenly across the joint makes it a safer and more effective option for these applications, ensuring the bond is strong without compromising the surrounding material.
Conclusion
The rosette-shaped heat stake post offers a range of benefits that make it the preferred choice for certain high-precision, high-stress, and aesthetic-sensitive applications. From enhanced bond strength and controlled material flow to improved resistance to torsional forces and minimized flashing, this design brings significant advantages to manufacturers in industries such as automotive, aerospace, consumer electronics, and medical devices. By choosing rosette-shaped posts for heat staking, manufacturers can achieve stronger, more durable, and visually appealing assemblies that meet the rigorous demands of today’s cutting-edge products.