In the electronics manufacturing landscape, Printed Circuit Board Assemblies (PCBAs) form the backbone of virtually every modern device. With the push toward more compact, efficient, and durable electronics, manufacturers are continuously exploring innovative techniques to assemble and secure electronic components. Among these techniques, heat staking has emerged as a critical process, offering unique advantages that align perfectly with the demands of PCBA manufacturing.
Understanding Heat Staking
Heat staking is a technique used to join thermoplastic parts with non-plastic components, such as metal inserts, rigid PCBs, or electronic devices. It involves applying localized heat to the plastic part, causing it to soften and reform around the non-plastic component. As the material cools, it hardens into a secure and stable connection. This process creates a durable mechanical bond without the need for adhesives or mechanical fasteners, making it an ideal choice for various PCBA applications.
Why Heat Staking Matters in PCBA Manufacturing
The advantages of heat staking extend far beyond its ability to create strong bonds. Let’s explore the specific benefits it brings to PCBA manufacturing:
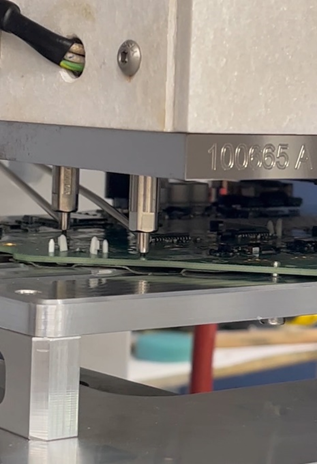
- Robust Mechanical Connections: PCBAs must withstand various mechanical stresses, including vibrations, shocks, and thermal expansions, especially in applications like automotive, aerospace, and industrial equipment. Heat staking provides robust mechanical connections that maintain their integrity under these conditions, ensuring the reliability and longevity of the assembly. This is particularly beneficial when securing components like connectors, headers, or large capacitors, where a solid attachment is crucial.
- Elimination of Additional Fastening Materials: One of the significant benefits of heat staking is that it eliminates the need for additional fastening materials such as screws, nuts, or adhesives. This reduction in material usage not only lowers manufacturing costs but also simplifies the assembly process. The streamlined approach enhances production efficiency, particularly in high-volume manufacturing settings where time and cost savings are critical.
- Compatibility with Automated Manufacturing: The heat staking process can be easily integrated into automated production lines, allowing for precise control over the staking parameters (temperature, pressure, and time). This compatibility with automation enhances production speed and consistency, reducing the potential for human error and ensuring uniform quality across all assemblies. As a result, manufacturers can achieve high throughput without compromising on quality.
- Minimized Risk to Sensitive Components: Heat staking is advantageous in PCBA manufacturing because it localizes heat application to the specific area where bonding is required. This targeted approach minimizes the risk of damaging sensitive electronic components, unlike soldering or other bonding methods that may expose the entire assembly to high temperature. Thus, heat staking helps maintain the electrical and functional integrity of the components and the overall assembly.
- Environmental and Thermal Durability: Heat staked connections offer excellent resistance to environmental factors such as humidity, temperature variations, and chemical exposure. This makes them suitable for applications where PCBAs are exposed to harsh conditions, such as in automotive engine compartments or outdoor electronic devices. The durability of these connections helps extend the lifespan of the PCBAs, providing long-term value to end-users.
Applications of Heat Staking in PCBA Manufacturing
Heat staking finds use in various critical applications within PCBA manufacturing:
- Securing Connectors and Components: By heat staking connectors, sensors, and other components directly to the PCB, manufacturers ensure a reliable attachment that can endure mechanical stress and prevent loosening over time.
- Mounting PCBs to Enclosures: Heat staking is often used to secure PCBAs to plastic enclosures or housings, especially in portable and handheld devices. This ensures that the PCB remains securely mounted, even with regular handling or exposure to vibrations.
- Anchoring Component Leads: In some designs, components with long leads may require additional support to prevent movement during use. Heat staking can effectively anchor these leads to the PCB, providing stability and preventing potential damage or electrical shorts.
Conclusion: Heat Staking – A Cornerstone for Reliable PCBA Assembly
In the world of electronics manufacturing, where precision, reliability, and efficiency are paramount, heat staking stands out as a versatile and valuable technique. By providing robust mechanical bonds, reducing material costs, and enhancing automated production, heat staking addresses many of the challenges faced in PCBA manufacturing.
As the demand for more compact, durable, and complex electronics continues to grow, the importance of reliable assembly techniques like heat staking cannot be overstated. Manufacturers leveraging the benefits of heat staking are better positioned to produce high-quality PCBAs that meet the rigorous demands of modern electronics, from consumer gadgets to industrial machinery. In summary, heat staking is more than just a method for joining materials – it’s a critical process that contributes to the overall quality and reliability of electronic products, paving the way for innovation and excellence in PCBA manufacturing.
At Thermal Press International (TPI), we take pride in designing machines that offer the accuracy and repeatability necessary to meet the stringent requirements of heat staking in precision manufacturing. Our equipment enables manufacturers to achieve precise heat staking requirements, resulting in tangible savings and improved product performance.
Contact Us: Contact Thermal Press International at (925) 454-9800 to speak with an engineer and explore how heat staking can optimize your manufacturing operations.