Heat staking stands as a fundamental process in modern manufacturing, offering a reliable means to mechanically lock thermoplastic components in place through controlled heating and reformation. This overview will delve into the intricacies of heat staking, providing insights into its methods, design considerations, and disassembly techniques.
Introduction: Heat staking involves the precise application of heat and pressure to melt and reshape a thermoplastic stud, facilitating the secure attachment of similar or dissimilar materials. Widely employed across diverse industries such as automotive, appliance, electronics, telecommunications, and medical sectors, heat staking proves indispensable for assembling components efficiently and economically.
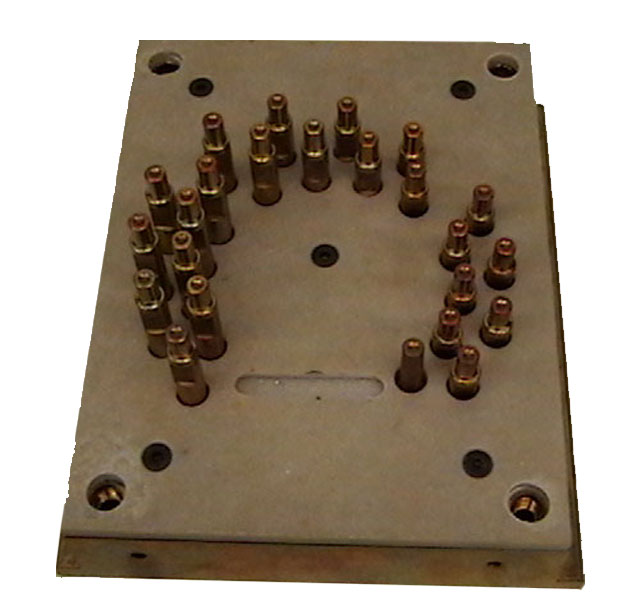
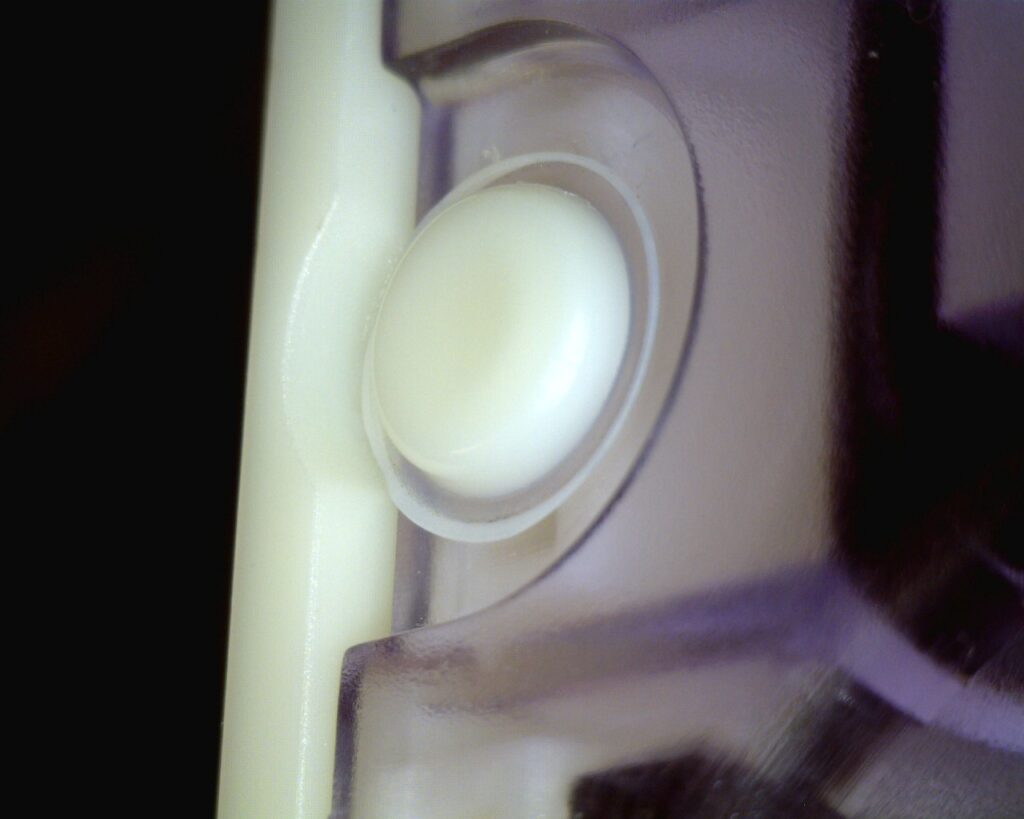
Heat Staking Design Tips: Successful heat staking begins with meticulous design considerations. By integrating post design and material selection into the initial development phase, manufacturers can achieve consistent, high-quality results. The direct-contact method, employing heated probes and pressure, emerges as a preferred approach for clean, odorless staking without the drawbacks of traditional methods.
Heat Staking Direct Contact Method: Central to the direct-contact method is the utilization of heated probes in conjunction with pressure to compress and form studs, effectively joining plastic components or combining plastic with other materials. This technique offers versatility across various plastic materials, including ABS, polystyrene (PS), polypropylene (PP), polycarbonate (PC), and glass-reinforced nylon (GFN).
Heat Staking Design Considerations: Design guidelines for effective heat staking encompass crucial factors such as post diameter, height, and geometry. Optimal working heights, typically 1.5 to 2.0 times the post diameter, ensure desirable stud-head proportions. Different post geometries, including flat-tip, dimpled, cross-shipped, or rosette-shaped, cater to specific application needs, offering solutions for structural integrity, aesthetic appeal, and functionality.
Heat Staking Disassembly: The disassembly of heat-staked assemblies, whether for recycling or reworking purposes, demands precision in heat and pressure control. High-heat piercing with pointed probes facilitates the clean removal of stud heads, enabling efficient disassembly. Reassembly options include utilizing alternate holes with self-tapping hardware or performing a secondary staking operation on reworked parts.
Conclusion: Mastering the art of heat staking requires a deep understanding of material properties, design principles, and assembly techniques. With meticulous attention to detail and the right equipment, manufacturers can harness the full potential of heat staking for streamlined production processes and durable assembly solutions.