In the rapidly evolving world of electronics, flexible circuits and flexible electronics are gaining significant attention for their versatility and applications across industries like healthcare, automotive, consumer electronics, and aerospace. These circuits, characterized by their lightweight, thin, and bendable properties, enable innovative designs and functionalities that rigid printed circuit boards (PCBs) simply cannot offer. However, challenges lie in effectively assembling and securing these delicate components without compromising their flexibility and performance. This is where heat staking emerges as a valuable technique in the manufacturing process.
What is Heat Staking?
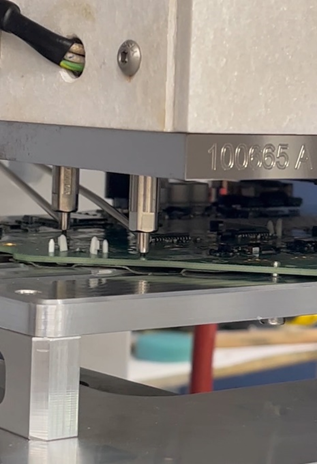
Heat staking is a process used to join a thermoplastic part to a non-plastic part (such as a metal, rigid PCB, or another flexible circuit) by melting and reforming the plastic around the non-plastic component. The process involves applying controlled heat and pressure to the thermoplastic material, causing it to soften and flow around the non-plastic part. Once cooled, the thermoplastic solidifies, creating a secure, durable and often watertight bond.
Why Heat Staking is Ideal for Flexible Electronics
Flexible electronics pose unique challenges due to their need for both robust mechanical connections and the ability to maintain flexibility. Heat staking offers several advantages that make it a preferred choice for assembling flexible circuits:
- Strong, Reliable Bonds: Heat staking creates a strong bond between the thermoplastic material and the non-plastic part(s), ensuring mechanical integrity without the need for adhesives or mechanical fasteners. This is particularly important in flexible electronics, where a secure connection is critical to maintaining functionality and reliability over time.
- Precision and Control: One of the standout benefits of heat staking is its precision. The process allows manufacturers to apply heat and pressure in a highly controlled manner, ensuring that the integrity of the flexible circuit is maintained. This precision is crucial for avoiding damage to sensitive electronic components and for creating consistent bonds across multiple assembly points.
- Material Compatibility: Heat staking is compatible with a variety of materials used in flexible electronics manufacturing, including polyimide films, PET, and other thermoplastics. This versatility enables manufacturers to utilize a wide range of materials to meet specific design and performance requirements.
- Maintains Flexibility: Unlike other bonding methods, such as soldering or using rigid adhesives, heat staking maintains the inherent flexibility of the circuits. The localized nature of the heat application ensures that only the areas needed for bonding are affected, preserving the flexibility of the rest of the assembly.
- Cost-Effective and Scalable: Heat staking is a cost-effective solution, especially for high-volume production. The process eliminates the need for additional materials like adhesives, reducing both material costs and assembly time. Moreover, heat staking equipment can be easily integrated into automated manufacturing lines, enhancing scalability and efficiency.
Applications of Heat Staking in Flexible Electronics Manufacturing
The value of heat staking extends across various applications within the realm of flexible electronics:
- Wearable Devices: In wearable technology, where flexible circuits are often embedded within fabrics or attached to flexible materials, heat staking ensures that electronic components remain securely in place, even when the device is subjected to constant movement and flexing.
- Automotive and Aerospace Applications: In automotive and aerospace industries, flexible electronics are exposed to extreme conditions, including vibrations, temperature fluctuations, and harsh environments. Heat staking provides a robust method for securing these electronics, ensuring reliability and longevity.
- Medical Devices: Flexible circuits used in medical devices, such as sensors and implants, require secure and biocompatible connections. Heat staking is ideal for creating precise and sterile bonds, ensuring patient safety and device performance.
- Consumer Electronics: From foldable smartphones to flexible displays, consumer electronics are increasingly adopting flexible circuits for innovative designs. Heat staking helps maintain the sleek and flexible profile of these devices while providing durable connections.
Conclusion: Enhancing Innovation with Heat Staking
As the demand for flexible electronics continues to grow, manufacturers are constantly seeking reliable, efficient, and scalable methods to assemble these advanced circuits. Heat staking stands out as a valuable technique, offering strong, precise, and cost-effective solutions that cater to the unique needs of flexible electronics manufacturing. By leveraging the benefits of heat staking, manufacturers can enhance their ability to innovate and bring cutting-edge, flexible electronic products to market faster and more efficiently. Heat staking is not just a bonding technique – it’s a gateway to the future of electronics, where flexibility meets durability and innovation knows no bounds.